So why alter, or process 3D parts?
As-built 3D printed parts typically suffer from 3 common drawbacks...
- Lack of (isotropic) strength
- Pourosity, and part inconsistencies
- Issues with scaling production economically
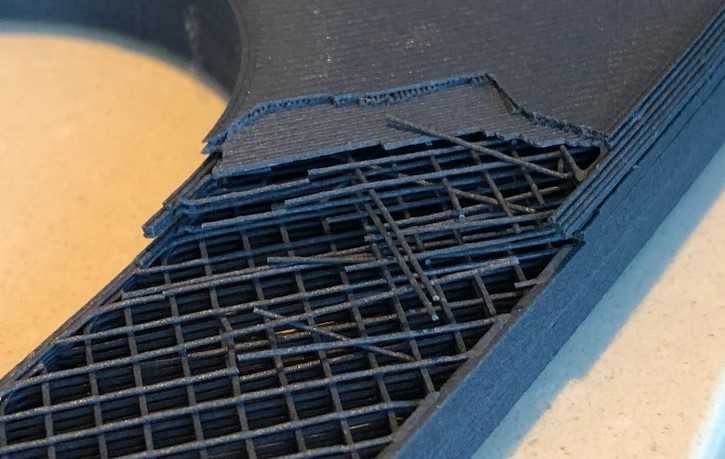
3D Fusion addresses each of these and more!
Before using 3D Fusion
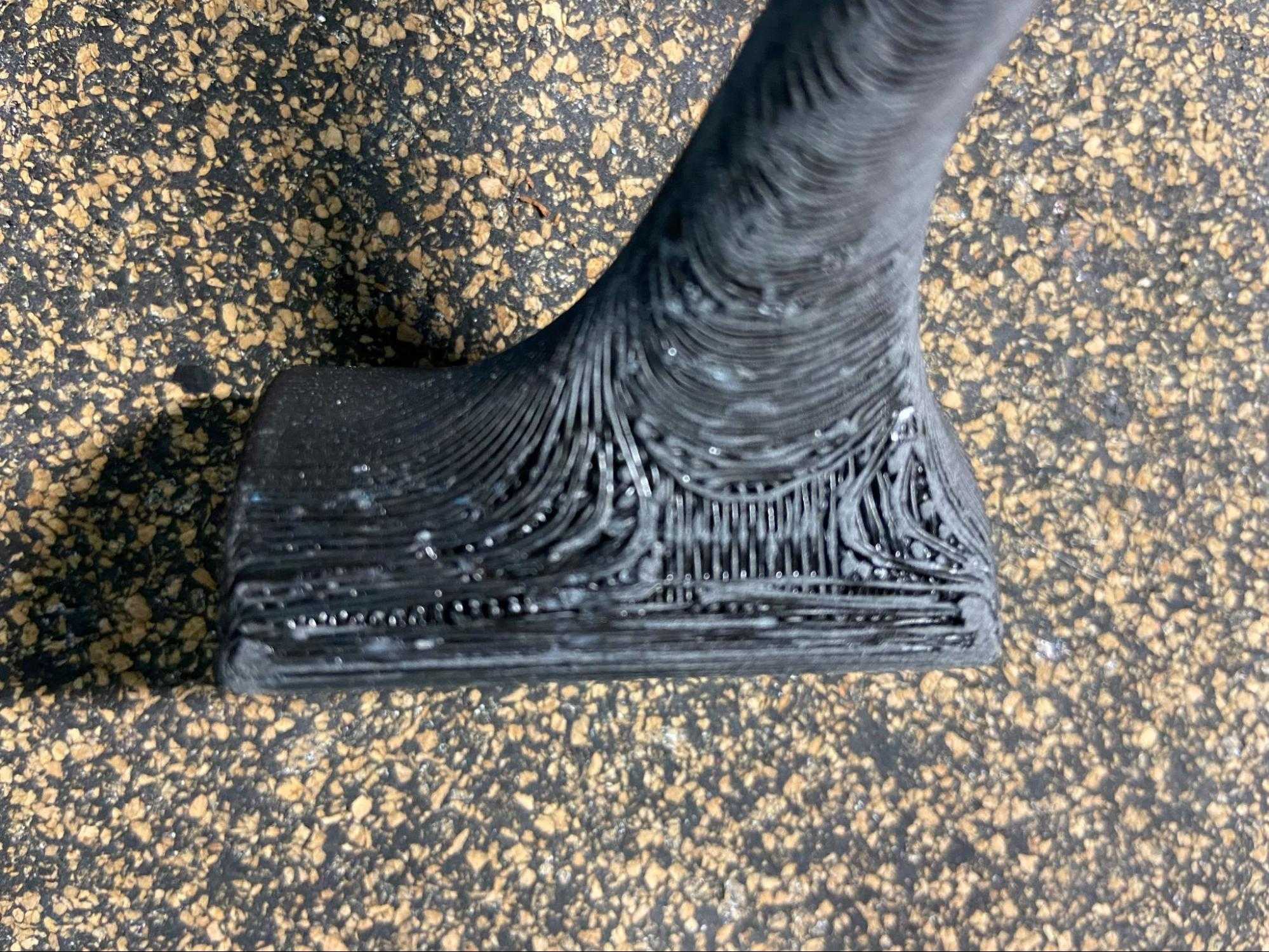
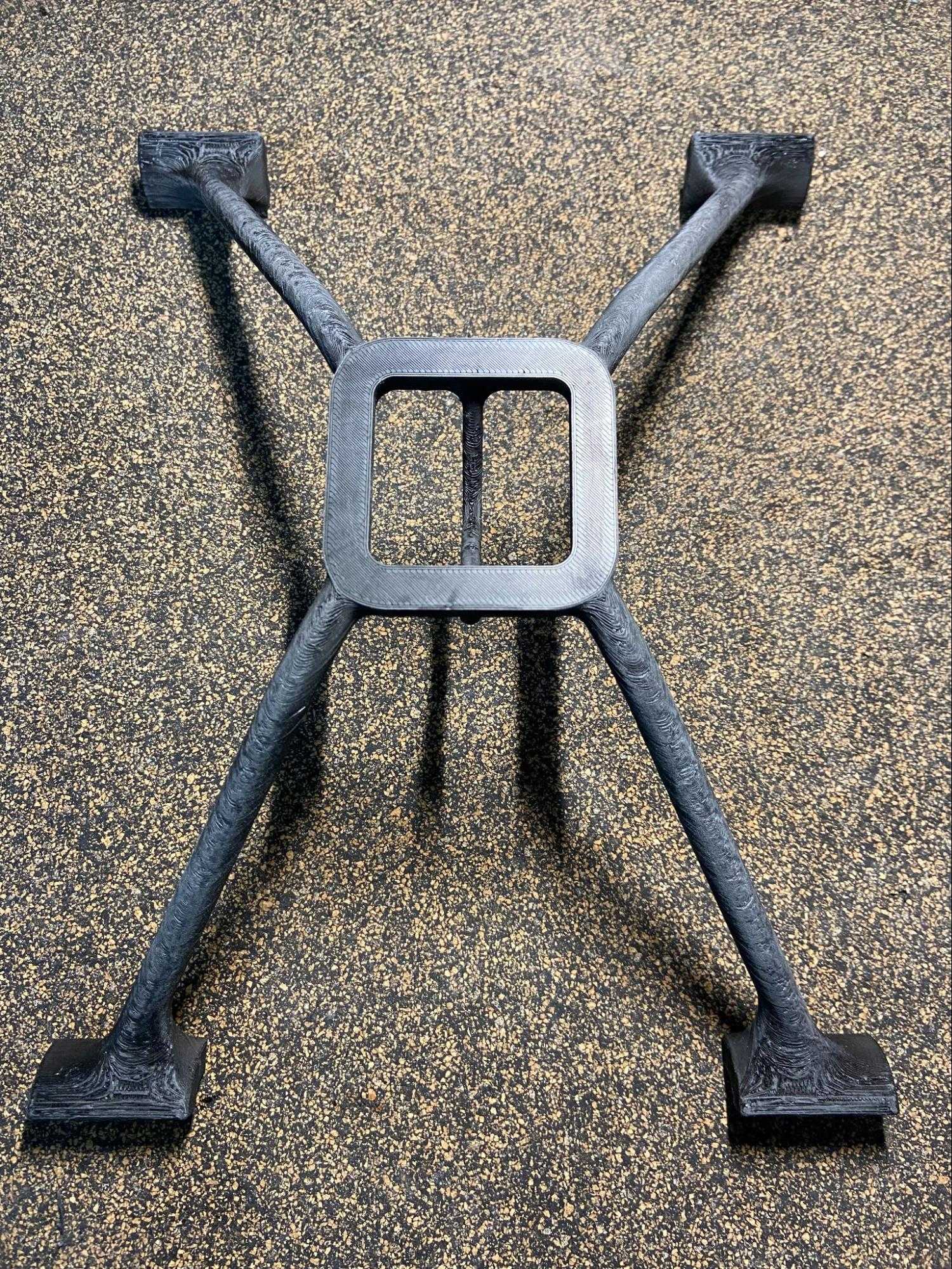
After using 3D Fusion
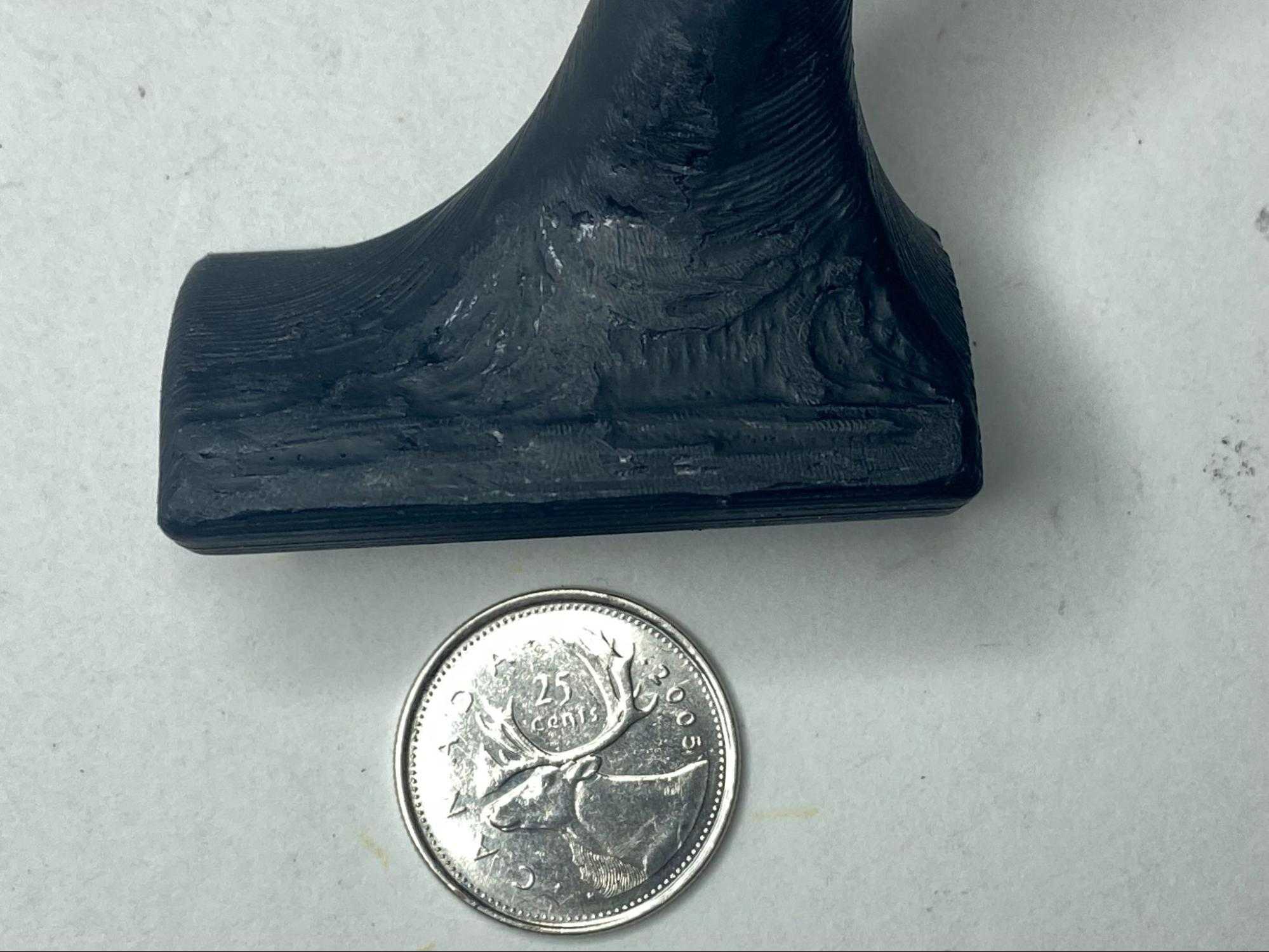
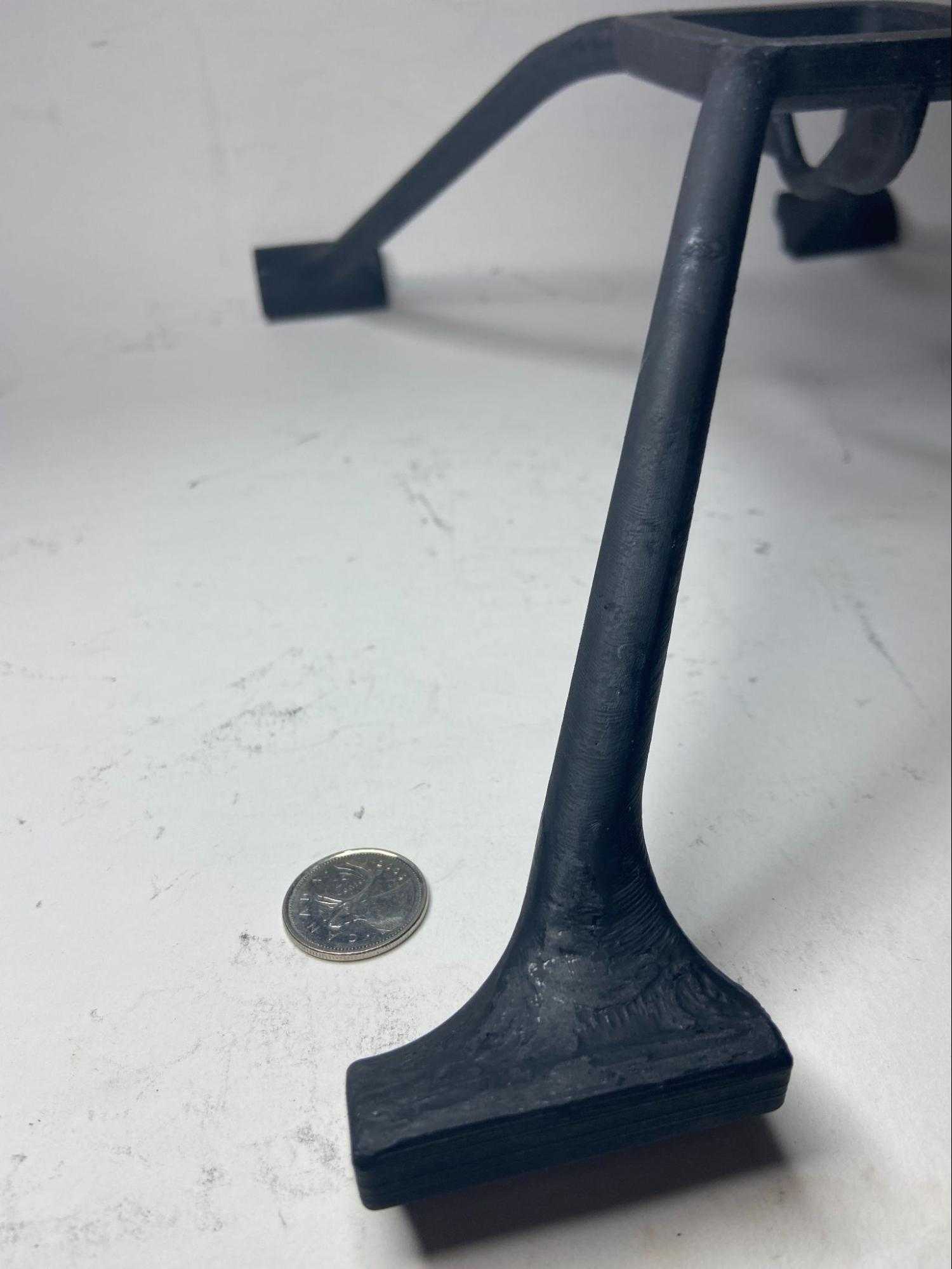
3D fusion post-printing processes
3D Fusion consists of 3 additive processes which are applied to parts after they have been 3D printed:
Freezing (frēziNG)
To hold at a fixed level or in a fixed state for a period of time.
- Generally speaking, Freezing increases the quality, consistency, and usability of 3D printed parts for home, industrial and commercial use, by fusing the plastic connections present in 3D printed parts, wherever they are. This bolsters and strengthens the as-built part, which likely harbors inconsistencies and flaws in the bonded plastic ribbons laid down during the 3D printing process.
- Not only is the part made strong across all axes (isotropic strength), but Freezing actually gives the part added stiffness when placed under low stress loads, and added flexibility under high stress loads. These are highly desirable characteristics.
- Freezing fills small gaps and fissures in the outer surface of the part making it smoother, more durable, and more attractive, without noticeably impacting dimensional accuracy. Freezing increases air and watertight qualities. Various other qualities may be added to parts in the Freezing process by simply changing the chemical formulation of the materials used ie. add UV Blocking, fire retardant, food safe, etc.
Casing (kāsiNG)
A cover or shell that protects or encloses something.
- The Casing process seals the outer surface of as-built 3D printed parts, and ensures air & watertight qualities. It does so by addressing flaws in the outer walls, ceiling, and floor surfaces which are left behind by the 3D printing process. It’s these flaws which are primarily responsible for porosity, and a lack of consistent strength in as-built parts.
- Casing strengthens the outer shell and improves adhesion between surface layers wherever flaws may exist.
- The Casing process measurably verifies air & watertight finish.
Loading (lōdiNG)
The application of an extra amount of something to balance some other factor.
- Loading of as-built 3D printed parts boosts the isotropic strength of those parts substantially. *The level of strength added is heavily dependent on the geometry and materials used in Loading the parts. Nevertheless, the results are nothing short of extraordinary!
- Mass, density, stiffness, and strength of (sparse-filled) 3D printed parts can be bolstered, manipulated, or customized to whatever degree is afforded by the part’s as-built geometry
- Loaded parts are air & watertight.
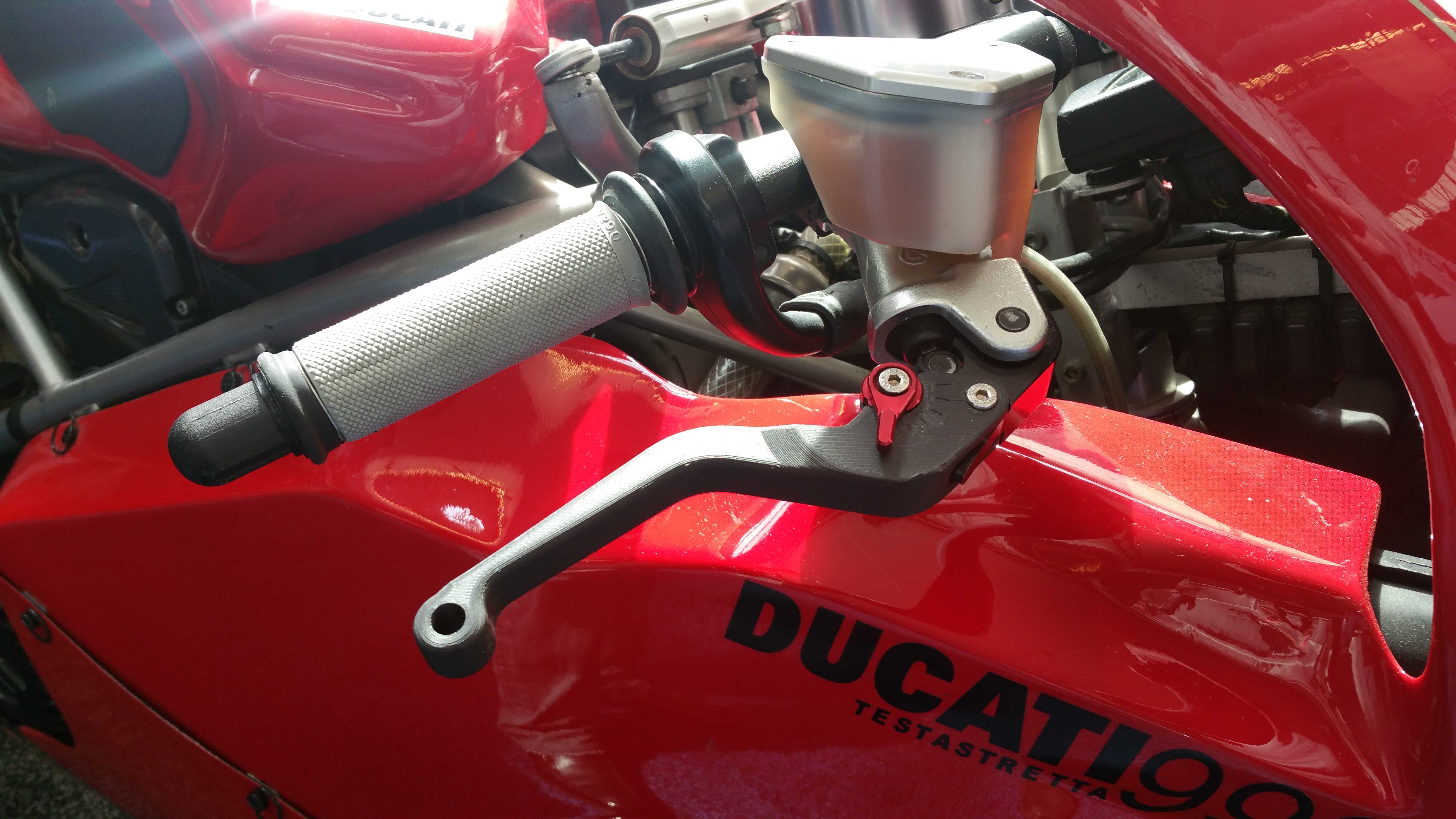
A fully functioning 3D printed part (brake handle) using our 3D Fusion technology.
3D fusion elevates printed parts
3D Fusion bolsters the as-built structure of 3D printed parts, elevating them to a new level physically, and chemically. 3D printed parts treated with these processes are enhanced with benefits and qualities not present in the original prints, as outlined in the descriptions above.
primary production benefits of 3D fusion
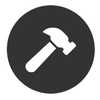
consistency
Combining 3D Fusion with 3D Printing elevates part consistency to Certifiable Standards.
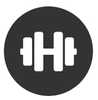
enhanced strength
3D Fusion enhances part strength across all axis and fuses all as-built structures into one.
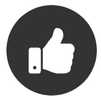
air & watertight
3D Fusion creates airtight and watertight qualities among the 3D printed parts (verified in process).
our 3D fusion technology at a glance
elevating 3d printed parts
It should be clear that the immediate benefits which flow from 3D Fusion are poised to elevate 3D printed parts (particularly FDM parts) to a new level of success in real world applications, well beyond that which the 3D printer platforms themselves are able to achieve (economically) on their own.
expanding commercial use of 3d printing
3D Fusion is complementary to the interests of both 3D print Users (Maker’s), and 3D Printer Manufacturer’s, as it will complement the hardware capabilities and help to define a path to expanded commercial use of 3D printed parts more generally.
sustainable manufacturing, unlimited possibilities
Finally, manufacturing itself will ultimately benefit from the new fabrication methodology prescribed here, because it opens the door to new production potential which is virtually unlimited in use, highly accessible, broadly distributed, and ultimately sustainable.
got a project?
make IT real!
We use 3D Printing combined with other novel and specialized AM methods to
make just about anything you can imagine!